We’re finally at the stage of committing to actual physical hardware, things that are going to be part of the finished VIXToscope… but we’re still transitioning to the stage of having high confidence that the designs translate to physical reality and buying lots of production things. This is a critical milestone where we move beyond POC (Proof of Concept — “yes, we see a way of doing something like what we’d imagined”) into prototyping (“This is going to be how we do it, or at least close, unless it erupts in flames and we have to reconsider…”) Its all a bit nerve-wracking, both from the perspective of committing increasing $$ to non-trivial amounts of physicality as well as realizing just how little time we have left before APOG — just 5.5 short weeks, yikes!!
I am racing to get all the designs firmly complete, ready to order from my sheet metal CAD company and the TSlot company, with full machining and very non-returnable parts. Kevin and I are also racing to complete all the LED designs, down to exactly what connectors and rainproof boxes we’re going to get. Some of this is settled, other bits are close, we’re moving very fast now and will probably have everything locked and ordered by the end of this weekend — which is luckily one more day than normal with Memorial day, thank goodness. I am sure I’ll need every minute.
I worked out the detailed designs for the LED strip sub-assemblies over the past few days. I was disappointed that it became impractical to order the LED channels and diffusors that I really wanted – they were beautiful, with a tall “U” shape to help the diffusion, and a really slick continuous clip system that looked very robust and would hide the screws into the TSlot (which also holds down the vinyl banner material “skin” of the structure) in a nice symmetric package. They were over $1,500 more expensive, had slower shipping, no returns, and the uncertainty of dealing with a Chinese supplier. So, we ended up with Amazon things (which came from China…), ranging from LED channel and diffusor to the power supplies and actual LED strips, along with connectors and everything else. As usual, Amazon is just too convenient to pass up even though I’d prefer to take my business elsewhere. Amazon is really great when you’re in a racing hurry and have low risk tolerance.
Both the original (fancy Chinese) and current (quick Amazon) designs feature an aluminum channel (a “U” shaped thin walled linear aluminum extrusion) that the LED strips go into with an “opal white” plastic bezel on top. The original had a tall “U” shaped bezel that would be visible from each side as well as the front; the current design is a “C” shaped top that is mildly visible from the sides but should look pretty dope even not quite as big as the original. I’ve left the render as a simple U, but the actual one will have a curved top.
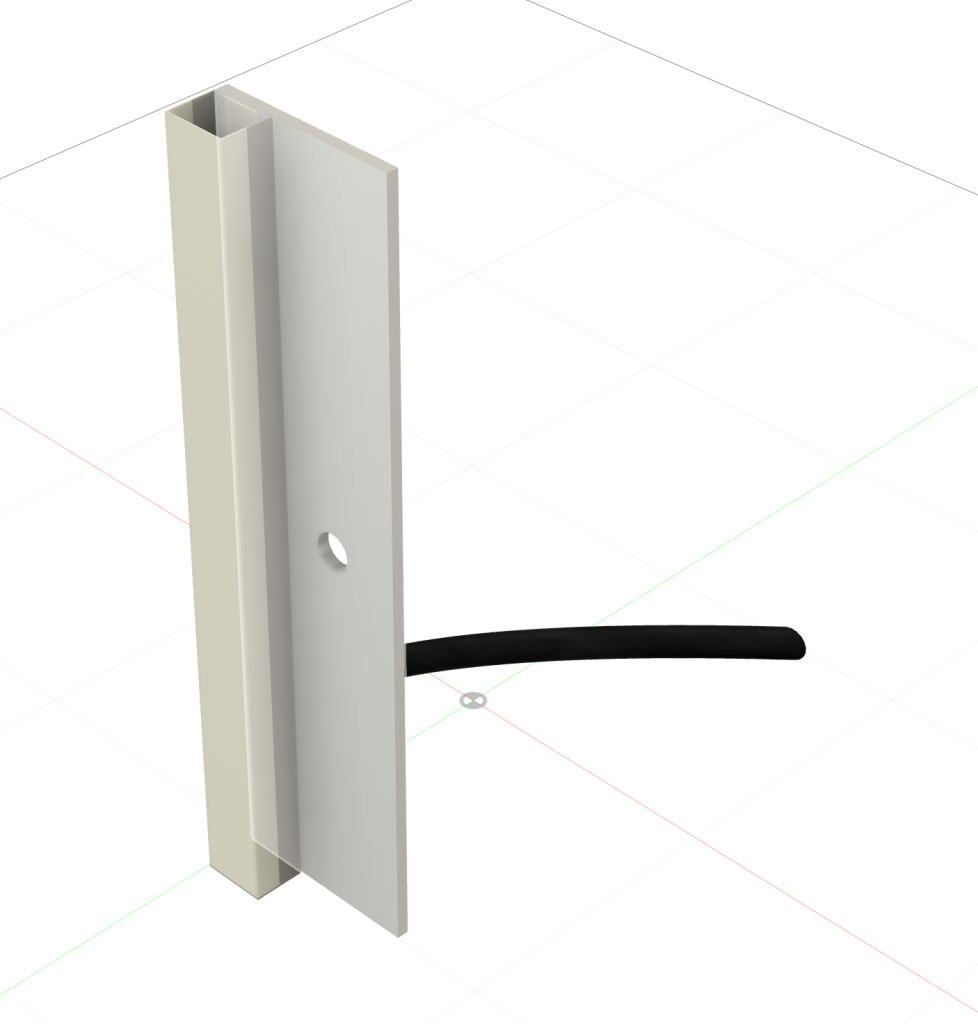
The biggest compromise was visible screws and an asymmetric arrangement on the aluminum backer. This goes on top of each TSlot prism truss. The original had a very slick mounting system that would have hidden the underlying screws and would have been in the center of the aluminum backer. Such is not be… so we ended up a design that makes for a bit wider backer strip — 2″ instead of the 1.5″ TSlot — with the channel offset to one side to allow enough space to put machine screws in to bind the vinyl banner and attach to the captivated TNuts in the TSlot. Instead of clipping the LED strip into the mounting plate on the backer, we end up just gluing the channel directly to the backer. This is still pretty slick (I hope).
There are SO MANY constraints I’m trying to optimize for, but two of the most important are DFP and DFM — Design For Playa, and Design For Moop. In systems design engineering, the job is basically weighing solutions against a bunch of constraints and trying to come out with something that approximates an “optimal” design by whatever criteria you determine are optimal. For example, DFM (Design for Manufacturing), DFR (Design for Repairability or Design for Reliability), and whatnot.
For me, its absolutely vital that this thing is easy to set up in the middle of an unforgiving, baking, windy, dusty, hot, enervating desert playa. Its also absolutely vital that the design make this as simple as possible to disassemble while leaving a provably zero amount of Moop – Matter Out Of Place. Small bits of wood, a small nut, a bit of plastic, a small piece of tape… any reminder that we were there with a giant art piece has to be eliminated with more or less 100% certainty. Part of this is in the process — things like a formal “moop sweep” — but more is in the original design. Design For Moop means minimizing anything that is small, fiddly, fragile or would be hard to ensure we had, intact, at the end.
So, my design for LED strips had to account for the crucial reality that I had to attach the vinyl banner material to the prism frame, and in a way that could be reasonably done in playa conditions, and survive playa conditions that include wind gusts up to 70MPH or even higher. The LED strips go over every truss, so a big part of their mission is to ensure the vinyl doesn’t rip off in a high wind, all while providing mechanical support for the fragile LED channels. Thus, the LED strip backer: a 2″ wide piece of 1/8″ aluminum, with laser cut holes to put 5/16″ machine screws into captivated TSlot nuts in the TSlot. By “captivated”, I mean installed in a fixed rather than loose/slidey way — the nuts are at a fixed position in the TSlot and won’t come out in the middle of the desert.
To do this, I’ll use set-screw TSlot nuts, and will apply a little glue once everything is confirmed with the test setup. The channel is then glued to the backer — I considered rivets and countersunk screws, but ended up with a flexible but incredibly tenacious polyurathane adhesive, Sikaflex 221. I’ve used this on my RV when installing solar panels, and its amazingly strong yet flexible. I blast down the road at 70mph with my Airstream’s solar panels held on by nothing but Sikaflex. Great stuff, and accounts for the inevitable flexing the pieces will undergo in setup/teardown/transport/storage – more rigid adhesives like epoxy or CA might work initially but give up after a few years with the stresses. I have absolute faith in Sikaflex’s ability to withstand decades.
So, on the playa, for setup — every nut is exactly where its supposed to be. Every aluminum backer has CNC-accurate holes to put in the machine screw. Each vinyl panel has holes with grommets at each place for the machine screw. Boom. In and done, no fiddling around in the hot, unforgiving sun. Vinyl and LEDS done, and very secure against wind blasts. When time to tear down, just remove: done, nuts are IN the TSlot and won’t fall out. Magnetic rake will catch any errant bolts or washers, but I doubt we’ll have them — magnetic raking last year turned up nothing for Gateway even though that was in terrible conditions and much worse DFP.
After settling on the overall design (asymmetric with the Amazon channels), the next practical consideration was getting cables into the channel, and providing strain relief. This is where I am *SO* thankful for having committed to OCD levels of CAD precision really paid off. I modeled LED strips on the precise aluminum backers, ensure the aesthetic design was solid, and stuck pigtails on the strips for the incoming power/control wire. Given the 2″ wide design on a 1.5″ TSlot, the channels had to be inset a bit; given the overlap of one channel over another, the end of the pigtail needed to be offset a bit; given the co-location of both pigtails at one corner, avoid conflict, ensure ability to go through an available grommet size (1″) into the vinyl… and we end up with a design modeled in CAD that gives me great confidence that it will work in the real world.
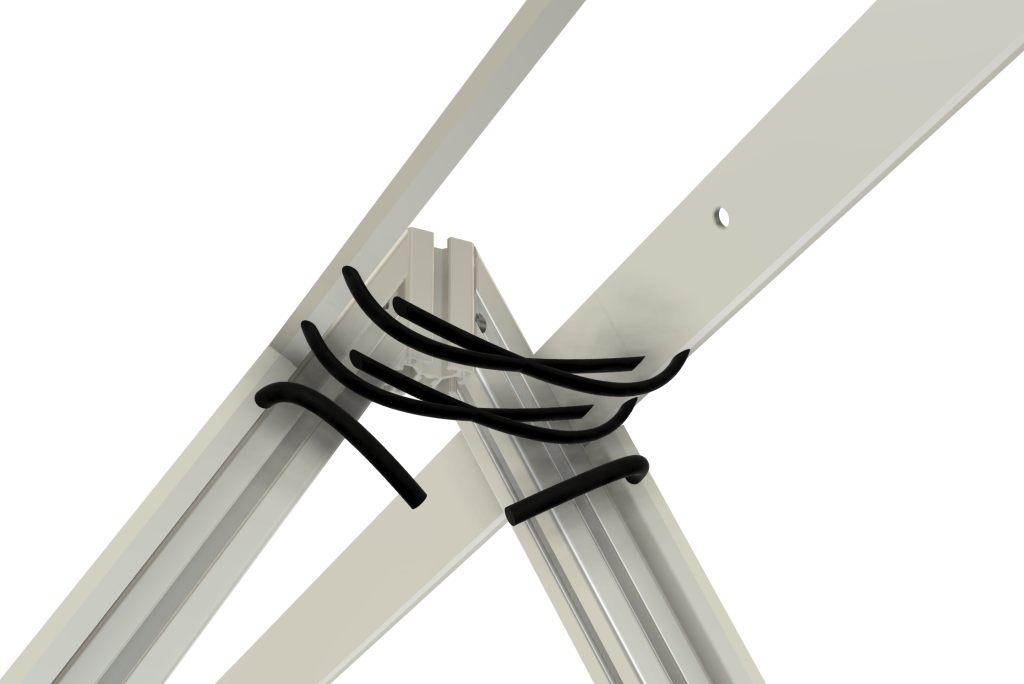
I eliminated the go-to strain relief, NPT glands, because they were too big for the channel. The only solution given the small, thin channel was to have an internal strain relief. I quickly sketched out a potential design, and Kevin immediately turned that into reality – and it worked fine. Mechanically sound, possible to efficiently solder and mass produce, destined for greatness I hope.
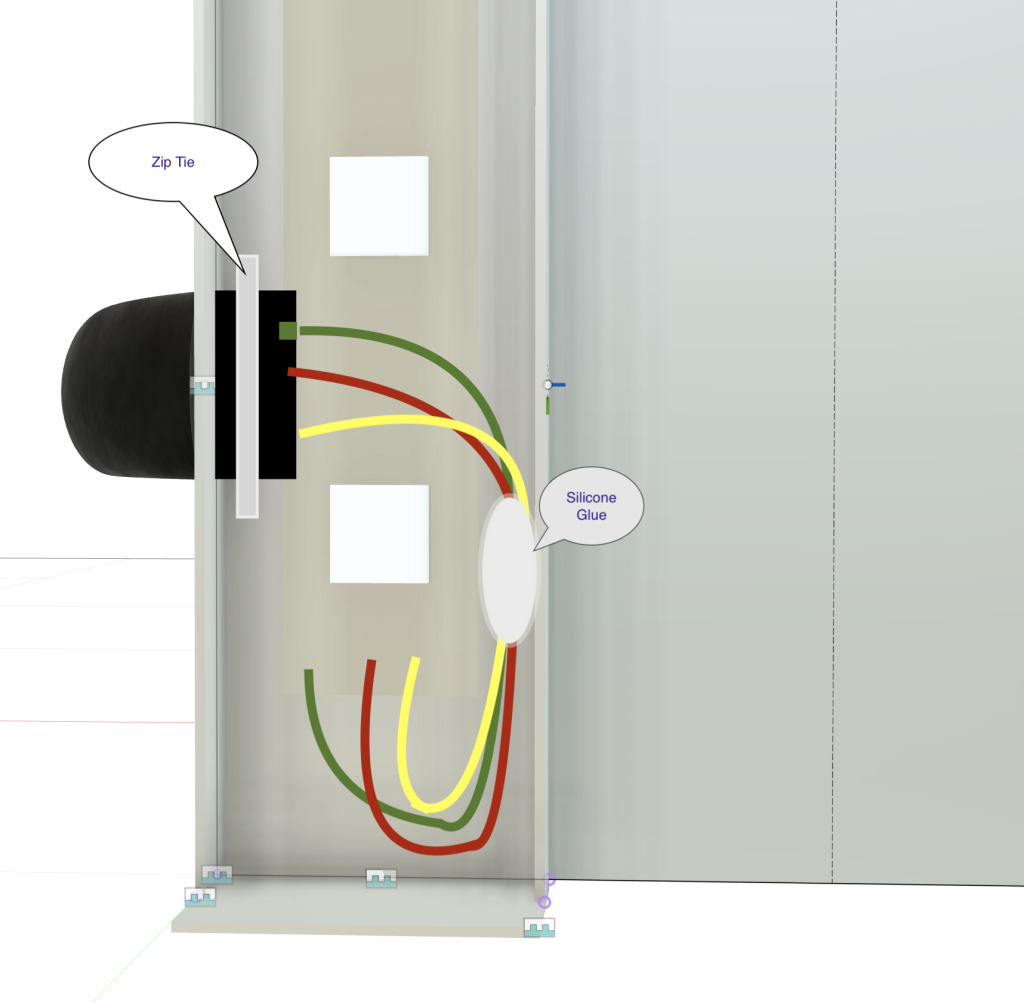
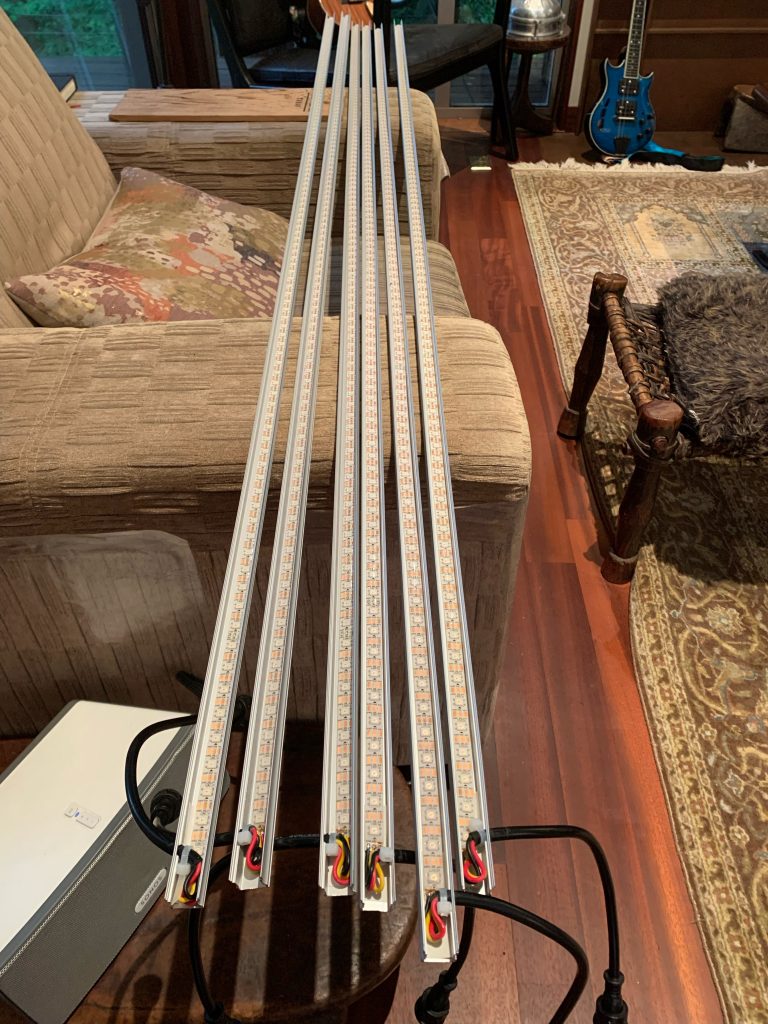

Next up: completing the Hub design, with bigger ESP32 box, only one gland, and a pressing hurry to be done. Tomorrow morning. Will allow modeling of every connection in the VIXToscope – how long, to where, with what connectors. Epic, don’t miss it.